Home : 32mm : Styles :
While shared panels can be used to build various styles of cabinets, full overlay panel designs can only be used to build full overlay cabinets. The full overlay style of Euro/frameless cabinetry is the most prevalent.
Full overlay cabinets are built as individual boxes that are stacked or butted and fastened together. The drawer and door faces are the same size as the box, less a small reveal. A typical perimeter reveal is 1.5mm so that when two boxes are placed next to each other there will be a 3mm gap (~1/8") between all faces.
When building full overlay cabinets you cannot use system holes as construction holes and unbalanced panels are usually a better option than the balanced panels common to other styles. You'll also be making/assembling a lot more pieces - the example drawing requires 2x (32 VS 16) as many pieces as a half-overlay or inset cabinet of the same design.
See also: Full-Overlay topics in the Drawers category.
If you want modular boxes, boxes that can be joined in any configuration while maintaining consistent gaps/reveals (as in the drawing above), there are only four possible panel designs. There are two reveal options and two indexing options. All full-overlay modular box/panel heights are a multiple of 32mm (sans feet and counter).
For the gap between the faces (door, drawer, etc.) of stacked boxes to be the same as the gap between all other faces, the sum of the box to face reveals (top + bottom) needs to equal the gap between faces (typically 3mm). You can have the faces flush to the bottom of the box (full reveal at the top, e.g. 3/0mm reveals) or split the reveal evenly between the top and bottom of the box (e.g. 1.5/1.5mm reveals).
Placing the full reveal at the top allows the gap between the top drawer/door and countertop, top mounted crown, etc. to be the same as the gap between the drawer/door faces. It also allows everything (applied ends, fillers, etc,) to be flush with the bottom of the box. This is really the only way to make stackable boxes that look and work good in all applications. The drawback is that unbalanced reveals equal unbalanced panels. With single head boring machines, boring balanced panels is more efficient. This is doubly true when drilling a single row requires multiple plunges of the head (e.g. 13 spindle machines).
Hardware, most notably drawer box offset, determines which is the best indexing option. For indexing to be a reliable constant, the top and bottom edges (plus 1/2 gap/reveal) of all faces need to be centered on a system hole (system) or at the midpoint between system holes (shifted). Shifted registration is most common (fourth drawing), but is not always the best option. True 32 was big on Zargon slides which work best with shifted registration. While Process 32 (see below) also uses shifted registration, most of their drawer layouts are broken.
As in the drawing, balanced reveal system row start holes can be 32mm (sys) or 48mm (shift) from the top and bottom of the panels. With all the reveal shifted to the top (faces flush to the bottom of the box), the bottom start holes can be 30.5 (sys) or 46.5 (shift) from the bottom of the panels (33,5 and 49.5 from the top, respectively).
[ comment | link | top ]
A thread on the Woodweb forum (now an article in the Knowledge Base) propted me compare some of the 32mm full-overlay panel designs. Kiss II, Danny Proulx, Process 32 and True 32 are panel designs that use the 32mm system (CabParts, The Pearls, Kurka and the "A Curriculum for Teaching 32mm Cabinet Construction" panels are not 32mm system panels). The primary difference between these and the Stackable Box designs is that they all have an increased reveal at the top of the panel (and aren't stackable).
For some folks its easier to bore balanced panels. The drawback of a balanced panel is that top and bottom face-to-panel reveals need to be the same. The top 1.5mm reveal of the balanced stackable-box design isn't enough when drawers and a counter are involved. It also looks best when all gaps are the same, e.g. between doors and crown molding/trim.
The Kiss II design is a balanced panel with 4.5mm top and bottom box-to-face reveals, i.e. 6mm taller than stackable box panels. I'm not sure how Joel decided on 4.5mm reveals, but that extra bottom reveal can allow for a better drawer layout - in a couple of select cases - and it does result in 30-1/2" tall panels for kitchens (VS 30-1/4" stackable panels, a pointless advantage IMO). The extra top reveal could allow for better top drawer counter clearance when bottom mount slides are used, but a 3mm reveal is typically fine (e.g. counter overhang can be up to 48mm/1-7/8" with Blum bottom-mount slides and a 3mm reveal). There's no way to justify the 4.5mm reveal aesthetically, its inconsistent and looks bad. Applied end panels and trim with a 1.5mm locating/mounting rabbet (light rail, crown, etc.) would be needed to hide the box (material/color match no longer critical) and provide a consistent 3mm gap between faces and trim (same as face to face gap). For same material boxes and faces, half-overlay is more consistent.
The Proulx design adds a whopping 32mm to the top of the balanced stackable box panel. The panel was designed specifically for 3/4" countertops with a built-down edge. A 19mm (3/4") built-down edge reduces the huge 33.5mm reveal to a large 14.5mm one. Its an interesting, though convoluted and aesthetically expensive, way (the only way) to have a balanced panel and unbalanced reveals... There is no rule/reason/advantage to n x 32mm box sides here. A 30.5/30.5 balanced panel (3mm shorter) would be better (0 VS 1.5 bottom reveal and 13 VS 14.5 top reveal). Using an unbalanced panel provides more options, e.g. add 20mm to the top of a 32.5/30.5 modular panel (52.5/30.5) to provide for a 19mm (3/4") counter build down and an extra millimeter of gap/reveal (4 instead of 3).
Unbalanced panels aren't a problem when one can bore at least a full system row with a single plunge/setting. The big advantage of unbalanced panels is that the faces can be flush with the box bottom (0mm bottom reveal). With a 0mm bottom reveal, the box edges are hidden and don't need to have the same wood/color/finish as the faces. When there is a big color difference between the boxes and faces (e.g white boxes and dark stained faces), the boxes can be edgebanded with a PVC that is similar in color to the faces.
Blum's Process 32 panels (unbalanced) are 7mm taller than the unbalanced stackable box panels. The reason for the extra reveal is that Blum is catering to folks who feel they must have American standards, e.g. 30-1/2" tall boxes and 4" toe-kicks instead of modular 30-1/4" boxes and 4-1/4" kicks. Only their bottom mount drawer layouts require the extra reveal and that is because their wood boxes are in 2" increments (most of their drawer layouts don't use the 32mm system).
While True 32 allows all stackable box panels, I included their Zargon panel here because the only difference between it and the Blum (not stackable) panel is the 10 VS 3mm top reveal.
[ page | comments (1) - Sunday, 30-Sep-2012 | top ]
Modular cabinetry is made with incrementally sized interchangeable components. The registration holes for assembling those components are all in the same (relative) position, regardless of the component incremental size or position in the cabinet.
The basis for the 32mm system is hardware with mounting holes some multiple of 32mm apart and drilling machines with multiple 32mm spaced drill bits. When using traditional line and construction drilling machines it makes sense to size and locate as may components as possible in 32mm increments. The only thing CNC changes is that increments other than 32mm can be used.
When using CNC to drill locating and assembly holes, the only dimension that has to to be in multiples of 32mm is the hinge plate and drawer slide mounting holes (f/b), When designing modular cabinetry, changing one dimension changes everything else on that axis.
Changing the vertical spacing of the slides to 31mm changes all height dimensions; panel, drawer box and face, door, hinge cup spacing, etc. While changing all vertical increments to 31mm provides dimensions that are closer to American standards, it has no effect on the constraints of modular cabinetry, e.g. the bottom drawers on full overlay cabinets... more
[ page | top ]
Full Overlay
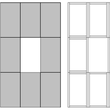
Full overlay cabinets are built as individual boxes that are stacked or butted and fastened together. The drawer and door faces are the same size as the box, less a small reveal. A typical perimeter reveal is 1.5mm so that when two boxes are placed next to each other there will be a 3mm gap (~1/8") between all faces.
When building full overlay cabinets you cannot use system holes as construction holes and unbalanced panels are usually a better option than the balanced panels common to other styles. You'll also be making/assembling a lot more pieces - the example drawing requires 2x (32 VS 16) as many pieces as a half-overlay or inset cabinet of the same design.
See also: Full-Overlay topics in the Drawers category.

Modular Panels
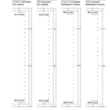
For the gap between the faces (door, drawer, etc.) of stacked boxes to be the same as the gap between all other faces, the sum of the box to face reveals (top + bottom) needs to equal the gap between faces (typically 3mm). You can have the faces flush to the bottom of the box (full reveal at the top, e.g. 3/0mm reveals) or split the reveal evenly between the top and bottom of the box (e.g. 1.5/1.5mm reveals).
Placing the full reveal at the top allows the gap between the top drawer/door and countertop, top mounted crown, etc. to be the same as the gap between the drawer/door faces. It also allows everything (applied ends, fillers, etc,) to be flush with the bottom of the box. This is really the only way to make stackable boxes that look and work good in all applications. The drawback is that unbalanced reveals equal unbalanced panels. With single head boring machines, boring balanced panels is more efficient. This is doubly true when drilling a single row requires multiple plunges of the head (e.g. 13 spindle machines).
Hardware, most notably drawer box offset, determines which is the best indexing option. For indexing to be a reliable constant, the top and bottom edges (plus 1/2 gap/reveal) of all faces need to be centered on a system hole (system) or at the midpoint between system holes (shifted). Shifted registration is most common (fourth drawing), but is not always the best option. True 32 was big on Zargon slides which work best with shifted registration. While Process 32 (see below) also uses shifted registration, most of their drawer layouts are broken.
As in the drawing, balanced reveal system row start holes can be 32mm (sys) or 48mm (shift) from the top and bottom of the panels. With all the reveal shifted to the top (faces flush to the bottom of the box), the bottom start holes can be 30.5 (sys) or 46.5 (shift) from the bottom of the panels (33,5 and 49.5 from the top, respectively).
[ comment | link | top ]

Other Panel Designs
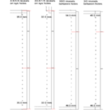
For some folks its easier to bore balanced panels. The drawback of a balanced panel is that top and bottom face-to-panel reveals need to be the same. The top 1.5mm reveal of the balanced stackable-box design isn't enough when drawers and a counter are involved. It also looks best when all gaps are the same, e.g. between doors and crown molding/trim.
The Kiss II design is a balanced panel with 4.5mm top and bottom box-to-face reveals, i.e. 6mm taller than stackable box panels. I'm not sure how Joel decided on 4.5mm reveals, but that extra bottom reveal can allow for a better drawer layout - in a couple of select cases - and it does result in 30-1/2" tall panels for kitchens (VS 30-1/4" stackable panels, a pointless advantage IMO). The extra top reveal could allow for better top drawer counter clearance when bottom mount slides are used, but a 3mm reveal is typically fine (e.g. counter overhang can be up to 48mm/1-7/8" with Blum bottom-mount slides and a 3mm reveal). There's no way to justify the 4.5mm reveal aesthetically, its inconsistent and looks bad. Applied end panels and trim with a 1.5mm locating/mounting rabbet (light rail, crown, etc.) would be needed to hide the box (material/color match no longer critical) and provide a consistent 3mm gap between faces and trim (same as face to face gap). For same material boxes and faces, half-overlay is more consistent.
The Proulx design adds a whopping 32mm to the top of the balanced stackable box panel. The panel was designed specifically for 3/4" countertops with a built-down edge. A 19mm (3/4") built-down edge reduces the huge 33.5mm reveal to a large 14.5mm one. Its an interesting, though convoluted and aesthetically expensive, way (the only way) to have a balanced panel and unbalanced reveals... There is no rule/reason/advantage to n x 32mm box sides here. A 30.5/30.5 balanced panel (3mm shorter) would be better (0 VS 1.5 bottom reveal and 13 VS 14.5 top reveal). Using an unbalanced panel provides more options, e.g. add 20mm to the top of a 32.5/30.5 modular panel (52.5/30.5) to provide for a 19mm (3/4") counter build down and an extra millimeter of gap/reveal (4 instead of 3).
Unbalanced panels aren't a problem when one can bore at least a full system row with a single plunge/setting. The big advantage of unbalanced panels is that the faces can be flush with the box bottom (0mm bottom reveal). With a 0mm bottom reveal, the box edges are hidden and don't need to have the same wood/color/finish as the faces. When there is a big color difference between the boxes and faces (e.g white boxes and dark stained faces), the boxes can be edgebanded with a PVC that is similar in color to the faces.
Blum's Process 32 panels (unbalanced) are 7mm taller than the unbalanced stackable box panels. The reason for the extra reveal is that Blum is catering to folks who feel they must have American standards, e.g. 30-1/2" tall boxes and 4" toe-kicks instead of modular 30-1/4" boxes and 4-1/4" kicks. Only their bottom mount drawer layouts require the extra reveal and that is because their wood boxes are in 2" increments (most of their drawer layouts don't use the 32mm system).
While True 32 allows all stackable box panels, I included their Zargon panel here because the only difference between it and the Blum (not stackable) panel is the 10 VS 3mm top reveal.
[ page | comments (1) - Sunday, 30-Sep-2012 | top ]

Custom Reveals
The only difference between modular boxes and other panel designs is the top and bottom drawer/door to carcase reveal. If you don't care about having stackable boxes, you can have whatever reveals you want. The only aspect of the 32mm system that changing top/bottom reveals affects is clearances - top and bottom drawer, counter, etc.
If you want to increase/decrease the reveal of a particular panel design, increase/decrease the panel height and distance to the top/bottom system holes by the amount of reveal you want to add/subtract. Top and bottom drawer clearances proportionately increase/decrease.
The height of a zero reveal (top and bottom) panel is always 32mm x n (32m) minus the gap you want between the door and drawer faces. Panel start (first t/b) holes are 32 - 1/2 gap for system registered faces and 16 - 1/2 gap for shifted faces.
When reveal is added to the equation, panel height is (32 x n) + top and bottom reveals - gap (32m + R - g). System registered top/bottom start holes are 32 - 1/2 gap + top/bottom reveal. Shifted registration top/bottom start holes are 16 - 1/2 gap + top/bottom reveal.
The table is based on a typical 3mm gap between door/door faces. The start hole distances are the minimum (practical) distance, actual start hole distances can be increased to the minimum needed to mount the hardware being used (+32m). See also: bottom clearance (companion table).
*When no applied ends are used, balanced panels provide a 1.5mm (1/2 g) perimeter reveal. Base cabinets (and uppers if crown is used) need at least a 3mm top reveal.
[ comment | link | top ]
If you want to increase/decrease the reveal of a particular panel design, increase/decrease the panel height and distance to the top/bottom system holes by the amount of reveal you want to add/subtract. Top and bottom drawer clearances proportionately increase/decrease.
The height of a zero reveal (top and bottom) panel is always 32mm x n (32m) minus the gap you want between the door and drawer faces. Panel start (first t/b) holes are 32 - 1/2 gap for system registered faces and 16 - 1/2 gap for shifted faces.
When reveal is added to the equation, panel height is (32 x n) + top and bottom reveals - gap (32m + R - g). System registered top/bottom start holes are 32 - 1/2 gap + top/bottom reveal. Shifted registration top/bottom start holes are 16 - 1/2 gap + top/bottom reveal.
The table is based on a typical 3mm gap between door/door faces. The start hole distances are the minimum (practical) distance, actual start hole distances can be increased to the minimum needed to mount the hardware being used (+32m). See also: bottom clearance (companion table).
reveal t/b | panel height | sys reg t/b | shift reg t/b | type |
t + b = R | 32m + R - g | 32 - 1/2 g + r | 16 - 1/2 g + r | |
0/0 | 32m - 3 (0R - 3g) | 30.5/30.5 (32 - 1.5) | 14.5/14.5 (16 - 1.5) | baseline |
Balanced | ||||
1.5/1.5 | 32m | 32/32 | 16/16 | modular/True 32 (sys) |
3/3 | 32m + 3 | 33.5/33.5 | 17.5/17.5 | increased reveals |
4.5/4.5 | 32m + 6 | 35/35 | 19/19 | KISS (sys) |
11/11 | 32m + 19 | 9.5/9.5 | 25.5/25.5 | half-overlay/System 32 (sys) |
33.5/1.5 | 32m | 32/32 | 16/16 | Proulx (sys) |
Unbalanced | ||||
3/1.5 | 32m + 1.5 | 33.5/32 | 17.5/16 | min. counter clear, no AE* |
3/0 | 32m | 33.5/30.5 | 17.5/14.5 | modular/True 32 (shift) |
4.5/0 | 32m + 1.5 | 35/30.5 | 19/14.5 | larger top reveal |
10/0 | 32m + 7 | 8.5/30.5 | 24.5/14.5 | Process 32 (shift) |
3(+19)/0 | 32m + 19 | 20.5/30.5 | 36.5/14.5 | 19mm build-down countertop |
*When no applied ends are used, balanced panels provide a 1.5mm (1/2 g) perimeter reveal. Base cabinets (and uppers if crown is used) need at least a 3mm top reveal.
[ comment | link | top ]

Modular CNC
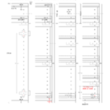
The basis for the 32mm system is hardware with mounting holes some multiple of 32mm apart and drilling machines with multiple 32mm spaced drill bits. When using traditional line and construction drilling machines it makes sense to size and locate as may components as possible in 32mm increments. The only thing CNC changes is that increments other than 32mm can be used.
When using CNC to drill locating and assembly holes, the only dimension that has to to be in multiples of 32mm is the hinge plate and drawer slide mounting holes (f/b), When designing modular cabinetry, changing one dimension changes everything else on that axis.
Changing the vertical spacing of the slides to 31mm changes all height dimensions; panel, drawer box and face, door, hinge cup spacing, etc. While changing all vertical increments to 31mm provides dimensions that are closer to American standards, it has no effect on the constraints of modular cabinetry, e.g. the bottom drawers on full overlay cabinets... more
[ page | top ]
