Home : Workshop : Metalwork : Mini Mill :
Many toolmakers vises have threaded holes that are handy for mounting material stops. A 10 series T-slot extrusion mounted to the vise is the best solution I have found for accurately machining long material.
I drilled incremental holes into the bottom of a t-slot and made a stop with dowels that mate with the t-slot holes. The end of the extrusion was tapped to match the vise (m8) and a setscrew was used to mate the two. Some careful shaving off the end of the extrusion was needed to get the slot with holes facing forward.
The stop shown is simple spring loaded block stop that is easy to move/position. There is a brief (10 sec) YouTube video showing how they work.
It's probably more common to machine something some distance from the end of the material (end VS center reference). In this case, the X-axis 0 point needs to be set some increment from the block stop. My usual 0 point is the left end of my vise so I measured the distance between it and the stop with an inside caliper (now written on the fence for future reference). Two increments from the stop was closer to the center of the vise so I subtracted the distance from the vise to the stop (my usual 0 point) from two increments, moved my table the difference and set my DRO to zero.
To position the workpiece, move the stop to the closest increment and then move the table the difference. In the example the desired distance from the left end of the material is 448mm. Since 448mm is 9mm less than a full increment (439), I moved the table from 0 to -9mm on my DRO. Note: Since part of this setup involved machining my 25mm increment fence, I used my 32mm fence. The increment size doesn't really matter unless you routinely machine at even increments (e.g. 32mm :-).
[ link | top ]
When using the center of the material as the reference point, start with the block as close as it can be to the end of the vice face. Move the table to align the milling head with the stop face and set the DRO to zero. Move the stop so that the center of the workpiece is as close to the center of the vise as possible. Add up the moved increments and subtract the total from half the length of the workpiece, move the head the difference (increments + move = 1/2 material length) and set the DRO to zero.
Here we are moving the stop to the closest full increment from the center of the workpiece and then moving the table the difference. In the example, the X-axis DRO is set to 47 (207mm hole - 160mm/5 increments), more than an increment because that is as close as the stop/end of the material could be to the zero point... That's not an example of how a center reference can be beneficial and it could have been avoided if the center point had been set one increment to the left.
[ link | top ]
Vise Fence and Stop
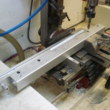
I drilled incremental holes into the bottom of a t-slot and made a stop with dowels that mate with the t-slot holes. The end of the extrusion was tapped to match the vise (m8) and a setscrew was used to mate the two. Some careful shaving off the end of the extrusion was needed to get the slot with holes facing forward.
The stop shown is simple spring loaded block stop that is easy to move/position. There is a brief (10 sec) YouTube video showing how they work.
End Reference
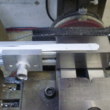
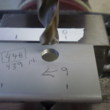
[ link | top ]

Center Reference
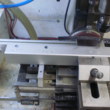
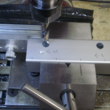
[ link | top ]
